The Sails Arrived!
A full set of used HD Sails arrived at my house on August 5th. Thanks to the MROA discussion forum, I was able to monitor the "for sale" postings. Rob Holroyd helped me narrow down my selection to a nice set of HD sails that Chris Martin was selling. Once Chris and I closed the deal it was easy to transfer him the funds from the US. Then, Andy Davis at HD Sails facilitated the logistics and 4 days later the sails were delivered in Austin, Texas. The full set included a main sail, a jib and a spinnaker. Thank you Roy, Chris and Andy!
The Gunwhales
The gunwhale is made from 3 laminations of Western red cedar. The inner section is triangular, the middle section is rectangular and the outer section is triangular. The inner lamination is fitted to the hull before the hull is removed from the frames.

The gunwhale and rubbing strake construction drawing provided by designer Keith Callaghan details the precise cross-section dimensions of the laminations at each station.
After cutting the initial triangular shape of the inner lamination, I marked the cross-section dimensions at each station and shaved off the excess material with the block plane. Firstly, I shaved the horizontal shape, secondly I shaved the vertical shape and thirdly I shaved the diagonal shape between the two.
Being this the first time I fitted a gunwhale lamination, it took me longer to get the process down. First I cut the sections of Western red cedar and tried to fit the lamination around the hull. Unfortunately the stock had several knots and, well, knots don't bend.
After consulting with Keith, he recommended I get rid of the knots and scarf the full length of the laminations. Why didn't I think about this? Too much heat, I suppose.

The steamer kit belongs to my friend John who is restoring his 23' gaffed rigged wooden sailboat. He placed wood dowels inside the pipe to keep the wood from touching the bottom and getting wet with the condensation.
Keith later told me that steaming was not necessary but it was a good learning experience for me.The wood did bend easier and left it drying over night before bonding.

Prepping The Hull

Later, I applied one more coat of epoxy resin over the entire hull. The wood patterns really came alive. It looked really great.

A view of the forward starboard side


A view of the aft port side.

Priming The Hull
The hardest part has been priming the hull after seeing the beautiful wood patterns after the final epoxy coat. But I had too many pencil markings and blemishes that wouldn't look good if varnished. So it is what it is.
Prior to applying the primer it is necessary to sand the hull, remove the amine blush on the epoxy with recommended chemicals and rinse the hull afterwards.

Following the hull preparation instructions, I applied to coats of Interlux's two-part Primekote primer, a multi-purpose two-part epoxy primer that is the recommended primer for use with two-part finishes.
The mix was a 3 to 1 ration based on Intelux's recommendation. To prime the Hazardous hull it took 12 oz. of part A, 4 oz. of part B and 4 oz. of Interlux's 2333n reducing solvent.
Starboard forward view

Aft port side
A view of the bow. The stem will be varnished and it is covered with blue tape.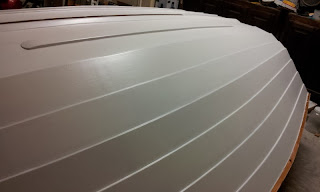
Aft starboard side. I'm leaving the gunwhale lamination unpainted for now until the other two laminations are fitted.
This primer is amazing. The specified mix and thickness was perfect. It adhered well to the hull without running. I used a foam roller to apply the primer.
With the heat we've been experiencing here in Austin this summer, it dried relatively quickly. I still waited 24 hours to apply the second coat.
All priming done and ready to be turned over... finally!
Turning The Hull Over
Rather than trying to lift the boat over the building frames I removed each of the building frames, one at a time, from the bow to the transom.


Once the centerboard is bonded to the hog and when ready to remove the building frames, a small piece of building frame #4 will have to be cut off to allow these components to pass through and clear the frame.

The building frames set to a side after being removed from under the hull. Anyone in the Austin, Texas area (or nearby) interested in building a Hazardous Merlin Rocket from Keith Callaghan? Buy a set of plans from Keith and you can have these building frames.

And it was the right decision. Once we had it sideways we could feel the self-righting momentum of the hull building up. Fortunately we were able to let it pivot around safely and placed it over the jig.
Before turning the hull over, I removed the building jig's legs and brought it down to the floor so I can have better access to the inside of the hull.
The Centerboard

Most of the frames came off easily except building frame #4. To the left you can see that I had installed the two 12 mm reinforcements on each side of the centerboard case top opening.
If these reinforcements and the lateral support "ears" are fitted during the initial centerboard case assembly process, the centerboard case can be mounted through the slots provided on the building frames.

Once the centerboard is bonded to the hog and when ready to remove the building frames, a small piece of building frame #4 will have to be cut off to allow these components to pass through and clear the frame.

A view from the transom after removing the aft building frames. I used 2" x 2" cedar stock across the jig to support the hull.


Here she is! My neighbor Danny came by to help me turn it over. At this point Keith believes the hull weights around 99 lbs. / 45 kg. The hull is very light but cumbersome to turn over by myself without damaging it. It was tempting but thinking about all the time spent working on it up to this point there was no way I was going to take that risk.

Before turning the hull over, I removed the building jig's legs and brought it down to the floor so I can have better access to the inside of the hull.
The Centerboard
The Centerboard Profile drawing provided by Keith Callaghan specifies the precise shape and measurements of the centerboard. Included within the full size drawing for Planks 1-4 is the centerboard drawing which can be used for making a full size pattern, which I did.

For the centerboard, I cut 1.5 m long X 25 mm thick X 40 mm wide strips of Western red cedar stock. I bonded enough strips to achieve the required width plus a couple of extra inches. I used clamps to hold the strips together and also 2' X 2" X 4" to hold the laminations flat.
I'm glad I did since some of the Western red cedar stock I cut bent and twisted a couple of days later. Some twisted so bad that could be suitable for floral arrangements.

The Rudder
The Rudder drawing provided by Keith Callaghan specifies the precise shape and measurements of the centerboard. Included within the full size drawing for Planks 1-4 is the centerboard drawing which can be used for making a full size pattern, which I did.


Next, I'll use the NACA foils document provided by Keith Callaghan to give them their final shape.